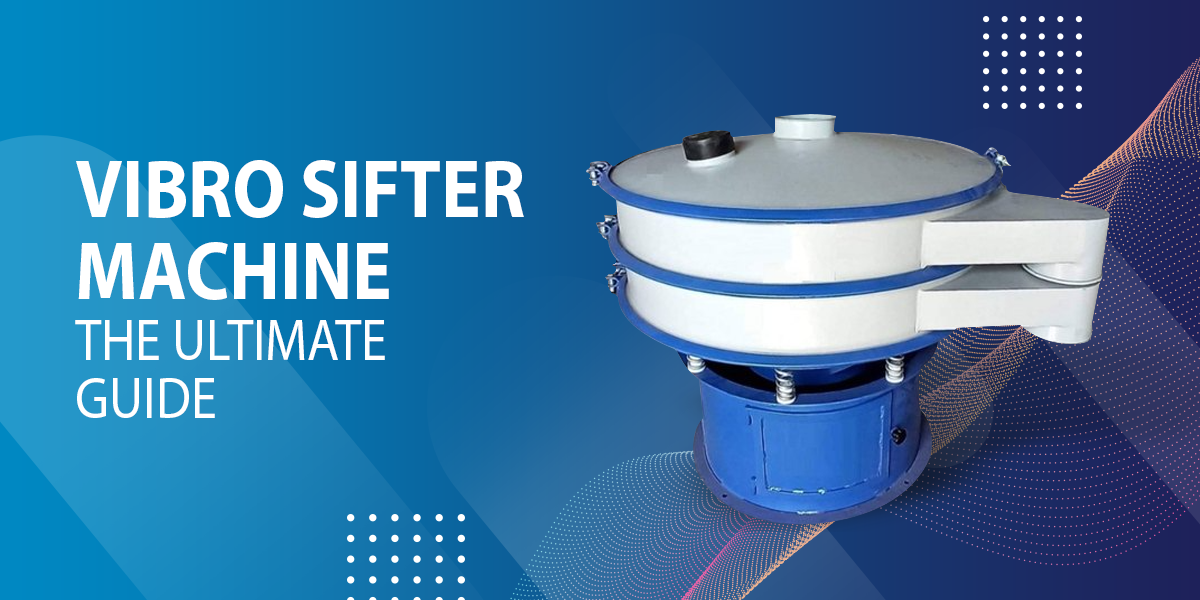
The Vibro Sifter is a machine that uses vibratory motion to separate materials or sift them. It is specifically intended to provide a score, scale, and sorting process that is applicable to all applications in the chemical, food, cement, and medicinal plant industries. This is a critical product that necessitates processing such as scalping, grading, and separating. The Vibro sifter process, which connects to the vibrational shifting product, is intended to act in isolation, scalping responsibilities, and gradient. Multiple components of the Vibro sifter are likely to contain copper wire, aluminum alloy, cast iron, lightweight plastic, and stainless steel that gives sturdy manufacturing materials.
A Vibro Sifter is a tool used in a variety of industries and labs to aid in the separation, grading, and scalping of materials based on the size of their particles. Essentially, it sieves particles that can be used as a final product or in future processes. Vibro sifter equipment comes in a variety of shapes and sizes.
What Is a Vibro Sifter Machine?
A Vibro sifter is a machine that uses vibratory motion to sift or separate different materials. As a result, it performs the separation and scalping operations more easily and efficiently.
It is sometimes referred to as a Vibro sieve or a safety screener. Other names for this device are check screen and vibrating sifter. A rotating screen, which can be circular or square, is used to grade and separate various materials, depending on what you want to accomplish with this process. For example, it will be used to separate solid materials from solids, solids from liquids, and particle gradation.
It provides these three major functionalities in a variety of applications for both wet and dry granulations. Aside from the Vibro sifter pharma, the use of this machine is common in various industries.
The chemical, cement, and food processing sectors are just a few of the industries that can benefit from the procedure. Even if your subject does not fall into one of these categories, you can still seek clarification from experts. A Vibro sifter machine's function is to sift materials during processing. This appears to imply that it primarily separates the mass composition of materials, making it one of the most important essential machines in production. This means that the equipment's design is intended to aid in obtaining proper product quality by removing large grains.
What Is the Main Difference between Vibro Sifter and Mechanical Sifter?
The source of energy is the main difference between a Vibro Sifter and a mechanical Sifter. A Vibro Sifter is powered by electricity, whereas a mechanical sifter is powered by hand. These two Sifters, on the other hand, rely on the vibrating principle to function.
What Are the Uses of Vibro Sifter Machine?

Although a Vibro sifter machine is commonly used for material separation, it is capable of much more. Furthermore, the sifter's application varies from one to the next. Here are some of the most common uses for a Vibro sifter:
1. Sieving
Fundamentally, as the name implies, this is frequently one of the initial applications of this type of processing machine. In fact, this simply refers to the removal of lumps or growths that may form in a substance as a result of prolonged storage.
What happens in this scenario is that the mesh opening is involved in the process that results in finer material. A practical example of sifting is flour, which you want to employ in your food manufacturing company. It occurs when strings, insect larvae, tags, and bug fragments are removed immediately after packaging or shipment before releasing the product to the buyer. As a result, in a substantial degree, this specific application is crucial and required to enable the final product to accomplish the stated features.
2. Screening and grading
Another important function of a Vibro sifter machine. The practice of separating a component based on its actual size is referred to as screening or grading. This is always visible when there is a relatively near task that requires excellent material separations. This activity is also known as bolting, sifting, sieving, or sizing in various cases. They essentially mean the same thing in this context, it's just that various people like to use different terminologies. Separating or sizing materials using vi can be quick or sluggish depending on a variety of parameters. Some of these factors include the type of material as well as its various qualities. The amount to which the fabric is processed is also a significant element in determining the pace of screening or grading. If your throughput is low, you'll need less screen real estate.
As a result, while utilizing this machine, you may recall the necessary modifications that you'll need to make in order to attain maximum efficiency.
3. Scalping
It entails the elimination of lumps or other forms of unwanted foreign particles from a more refined material. Twigs, tags, strings, and sticks, among other things, are examples of undesirable particles that can be removed with scalping. Typically, the dimensions of the mesh or opening are larger than the size of the actual product. As a result, scalping can occur at a current rate with a large amount of material on a small screen area.
Parts and Components of a Vibro Sifter
A Vibro Sifter manufacturers create various sections and components that work together to obtain the desired result.
Let's go through some of the most important Vibro Sifter machine parts you should be aware of:
1. Motor
This is the component that powers the entire computer, allowing it to run and conduct all activities without interruption. The vibrating sifter, understandably, makes use of electricity. As a result, the motor is responsible for transforming electrical power into energy that powers the unit. So, if you see continuous multi-plane vibratory motion, recognize that it is caused by the facility's electrical generating. It's critical because the vibratory action accelerates the passage of constituent particles through the various sieves. Obviously, the proportions of the motors for this machine vary based on the device's dimensions and design.
2. Filter Screen
This component is critical in ensuring that the fabric has a smooth surface finish during processing. It is built with a wire mesh that has a reasonably fine surface, which is helpful for sieving materials and producing exceedingly fine particles. Furthermore, by utilizing its performance, you will be able to avoid any instances of leakage throughout material processing. Filter screens are also available in a variety of sizes depending on the machine's design.
3. Hopper Lid
Hopper lid is a term that is used occasionally. It primarily protects the material being processed from the upper area so that it does not fall when the machine vibrates. The hopper in most Vibro sifter systems is often constructed of metal. Clearly, this aids in the prevention of contamination of the material. Because clamping rings maintain the lid in the appropriate position, it can remain integral and undamaged during processing. Furthermore, because the mesh is fairly fragile, the lid protects it from coming into contact with external objects that could damage it.
4. Wire Mesh Screen
It refers to a circular component that contains the wire mesh screen. The screen ring contains adhesive that aids in the bonding of the mesh, making it perfect for increasing the mesh's lifespan. Furthermore, the strong bonding ensures that the wire mesh remains intact during material processing regardless of the unit's vibration intensity.
5. Screen Material Outlet
This is a chute that discharges all graded, screened, or sized granules from the machine for further processing if necessary. This vibro sifter component is located at the bottom of the filter screen. This is critical because it allows all of the screened particles to easily congregate and exit the machine.
6. Springs
Springs are commonly used to improve the hydraulic movement of a Vibro sifter. They keep the unit's upper half intact while it vibrates to separate the materials. In a larger sense, the springs serve as a damper. This allows the machine to freely vibrate. In this scenario, it prevents the vibration from being transmitted to the ground. Springs in this machine also aid in properly placing the machine to provide the desired efficiency during material processing.
7. The Control Panel
This is arguably one of the essential components of this type of sieving machine. It is a component with which you will most likely interact. A control panel is often made up of various buttons that transmit a signal to the equipment indicating what action it should perform. It is an essential component since it incorporates technology, which greatly influences many parts of the machine's rotational operation. In certain machines, the instrument panel has an LCD touchscreen display from which you may control the entire machine's capabilities. While these are the basic components of a Vibro sifter machine, there are other minor components that are more technical.
What is the Working Principle of Vibro Sifter?
To understand how to utilize a Vibro Sifter, you must first understand how it works. Here's a step-by-step guide on using this machine.
Step 1: Begin by placing the items to be separated on the machine's feeding hopper. Confirm that the bottom frame, cover, and screen structure are all fastened with the clamping rings at the same time.
Step 2: Now, turn on the facility's power supply. This appears to provide energy to the motor, allowing it to vibrate as a result of the off-balance weight assembly.
Step 3: The sieve will then begin to vibrate vigorously. As a result, the grains on the hopper move through the sieves and pass through an equivalent counting on the specified.
Step 4: The equipment has exit components that discharge the materials once they have travelled via a controlled passage. This occurs immediately following the effective separation of materials, such as the larger ones being expelled from the smaller ones. Keep in mind that the particle size will be determined by the size of the screen.
Step 5: Once you've completed the entire process, you'll restart from the beginning. You only need to perform the technique each time you want to separate your materials.
The working principle of the vibro sifter machine can be altered based on the qualities of the materials to be processed. Otherwise, this is typical Vibro sifter technique.
Factors to Consider When Buying:

Not every Vibro sifter for sale is the same. They are available in a variety of designs, and their processing capacities vary. So, which Vibro sifter is the best on the market? Here are some of the most important elements to consider while purchasing a Vibro sifter in China.
1. Specific Vibro Sifter Application
For what purpose do you plan to use the vibro sifter? That should be your first consideration. This machine can be used for a variety of purposes. It can also be used in scientific investigations and industrial processes. So the Vibro sifter you select should be the deciding factor in each case?
A fairly small-sized Vibro sifter would be appropriate for small-scale applications. You'll need a rather large Vibro sifter for industrial applications.
If you do your search properly, you will be able to find all sizes in the market.
2. Vibrator Sifter Machine Design
Essentially, the general design of a vibro sifter is determined by the manufacturer. This implies that each Vibro sifter maker creates their own distinctive designs in the hopes of gaining a footing in the market.
For example, you can discover a machine that has an L-shaped sieve frame design but also has a distinctive separable design.
3. Number of Filters
Depending on the application, this machine can be used in a single, double, or triple layer. However, the number of sieves required by your machine is also linked to the degree of product separation it is built for.
What Are the Advantages of Vibro Sifter?
A Vibro Sifter is a productive manufacturing machine that filters and separates materials in a certain size based on the need for further processing and direct use. It is critical to remember that the machines can employ the vibratory sequence to separate to produce better results. Manufacturing machinery comes in a wide variety of shapes, sizes, and designs. As a result, it is critical to consider the following benefits:
• Portable and compact in size
• Better functionality to handle the dust particles
• Energy-efficient manufacturing machinery
• High-speed service with guaranteed minimum noise
• Multiple screen variation
• Vibratory motion in the adjustable mode
• Easy-to-clean and dismantle
• High-quality performance guaranteed
• More usability in a flameproof motor component
• The long span of services
Conclusion
The Vibro Sifter machine is an efficient piece of industrial machinery that separates and sieves the components to the desired particle size for further processing and direct usage. A vibratory motion is used to separate materials in order to achieve the desired product outcome. As a result, it is critical to invest in high-quality, energy-efficient equipment.
How do you differentiate between Vibro Sifter and Mechanical Sifter?
Related Products
You Might Like Also
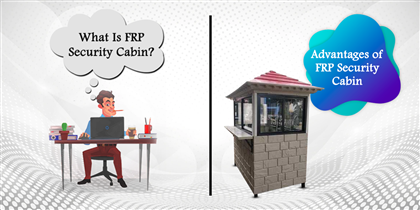
FRP Security Cabins are a great way to add extra space to residential and business buildings. They take less time to build, come in a variety of shapes and sizes, and can be easily moved from one location to another. Read More
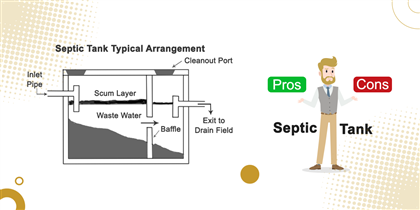
A Septic tank is a sewage treatment system that comes with various types. Its operating mechanism includes bio septic tank safeguards. However, there are pros and cons in terms of maintenance and repairs. Read More