Bead blasting is a versatile surface treatment process often used to clean, smooth, or enhance materials. While it’s commonly applied to metals, it can also work effectively on plastic components. By using fine media like glass beads, this process removes imperfections, improves surface texture, and prepares plastics for painting or coating. However, due to the softer nature of plastics, careful adjustments to bead size and pressure are essential to avoid damage. When done correctly, bead blasting offers a practical solution for improving the performance and appearance of plastic parts across various industries.
This article explains the applications of bead blasting in plastic manufacturing, the type of plastic compatible with bead blasting, and the pros and cons of bead blasting for plastic. It also gives tips for a safe and effective bead blasting.
Applications of Bead Blasting in Plastic Manufacturing
Here are the applications of bead blasting in plastic manufacturing:
Surface Preparation
Bead blasting plastic is widely used to prepare plastic surfaces for secondary processes such as painting, coating, and adhesive bonding. Plastics often have smooth or glossy surfaces, making it difficult for paint or adhesives to stick. Bead blasting gently roughens the surface, creating an ideal texture for better adhesion. This step ensures uniform application and helps coatings resist wear and peeling. This process guarantees durable and visually appealing professional finishes in industries like automotive and electronics.
Deburring and Edge Smoothing
Manufacturing methods like injection molding and machining often leave plastic parts with unwanted burrs or sharp edges. These imperfections can compromise the part’s function, make assembly difficult, or pose safety risks. Bead blasting is an effective way to remove burrs and smooth edges, leaving parts clean, safe, and ready for use.
Unlike other methods, it preserves the integrity of the plastic, ensuring the component retains its dimensions. For medical devices or precision components, where even minor defects can be critical, bead blasting provides a reliable solution for quality enhancement.
Finishing
Plastic components often require specific textures for aesthetic or functional purposes. Bead blasting creates a consistent matte or satin finish, enhancing the visual appeal of products like consumer electronics, automotive interiors, and home appliances. In addition to looks, this process can reduce glare, improve grip, or provide an anti-slip surface. Custom textures can also be achieved by varying the bead size and blasting pressure, giving manufacturers flexibility in design. This makes bead blasting ideal for creating high-quality, visually appealing plastic products.
Cleaning
Bead blasting effectively removes contaminants like grease, mold release agents, or residues from plastic surfaces. This is particularly useful in industries such as medical devices or food packaging, where cleanliness is critical. By eliminating surface contaminants, bead blasting ensures that the parts meet strict quality and safety standards. The process is also non-abrasive when done correctly, meaning the plastic remains undamaged while being thoroughly cleaned.
Types of Plastics Compatible with Bead Blasting
Not all plastics respond equally well to bead blasting due to differences in hardness, heat resistance, and surface characteristics. Here are some common types of plastics that are compatible with bead blasting:
ABS (Acrylonitrile Butadiene Styrene)
ABS is a durable, impact-resistant plastic commonly used in automotive parts, consumer electronics, and 3D-printed components. It can withstand the bead blasting process without cracking or deforming, making it an ideal candidate for surface smoothing, deburring, and texturing.
Polycarbonate (PC)
Polycarbonate is a strong, transparent plastic often used in applications like safety goggles, lenses, and automotive panels. It can handle low-pressure bead blasting for surface cleaning and preparation. However, care must be taken to avoid excessive heat, which could affect its optical clarity.
Nylon (Polyamide)
Nylon is known for its strength and resistance to wear, making it suitable for bead blasting. This plastic is often used in gears, bearings, and industrial components. Bead blasting can remove surface imperfections and create a smoother texture for these parts.
Acrylic (PMMA)
Acrylic, commonly used for signage, displays, and optical components, can be bead blasted to achieve a matte finish or remove minor surface defects. Low-pressure settings and fine media are essential to prevent cracking or clouding.
PVC (Polyvinyl Chloride)
PVC in pipes, fittings, and industrial parts is compatible with bead blasting for surface cleaning and deburring. Its hardness and stability under low-pressure blasting make it a reliable choice, though excessive pressure should be avoided to prevent deformation.
Delrin (POM - Polyoxymethylene)
Delrin, a type of acetal plastic, is widely used in precision engineering due to its low friction and high strength. Bead blasting can enhance the surface by removing machining marks and creating a uniform texture. Its resilience ensures it can withstand the process without damage.
HDPE (High-Density Polyethylene)
HDPE is a versatile and durable plastic often used in packaging, piping, and automotive parts. It is compatible with bead blasting for light cleaning and smoothing. However, its low melting point requires careful monitoring to avoid softening.
Benefits of Bead Blasting Plastic Components
Here are some of the bebnfyt of bead vlastic p;atsic compjnets:
Improved Surface Adhesion
One of the primary benefits of bead blasting is its ability to improve the adhesion of coatings, paints, and adhesives to plastic surfaces. By creating a slightly roughened texture, bead blasting enhances the surface area for better bonding. This is crucial for applications requiring a durable surface finish technology or strong adhesive bond, such as automotive parts, consumer electronics, and medical devices.
Deburring and Edge Smoothing
During the manufacturing of plastic parts, processes like injection molding or CNC machining can leave behind unwanted burrs or sharp edges. Bead blasting effectively removes these imperfections, leaving a smooth, polished edge without altering the dimensions. This is especially important for parts that must fit precisely, such as connectors or components in complex assemblies.
Enhanced Aesthetic Appeal
Bead blasting can create a matte or satin finish on plastic components, providing a uniform and visually appealing surface. This process is often used to improve the appearance of consumer goods, like housings for electronic devices, automotive interiors, and decorative elements. The smooth, consistent finish reduces glare and enhances the overall look of the part.
Cleanliness and Contaminant Removal
Bead blasting effectively cleans plastic surfaces, removing contaminants such as oils, mold-release agents, dust, and residues from previous manufacturing stages. This is particularly important in industries like medical device manufacturing, where cleanliness is critical to ensure product safety and meet regulatory standards.
Challenges in Bead Blasting Plastics
Here are some of the disadvantages of bead-blasting plastics:
Risk of Surface Damage
Plastics are generally softer than metals, making them more susceptible to damage from the abrasive media. If the blasting pressure or media type is too aggressive, it can lead to surface scratches, dents, or cracks. Fine-tuning the blasting parameters is essential to avoid harming the plastic's surface or structure.
Heat Sensitivity
Plastics, especially those with low melting points, are highly heat-sensitive. Bead blasting can generate heat due to friction, which may soften or distort the plastic. Overheating can lead to warping or dimensional changes, especially in parts that require precise tolerances. Managing the blasting pressure and duration is crucial to mitigate heat buildup.
Inconsistent Results
Achieving a consistent finish on plastic surfaces can be challenging. Variations in the plastic's composition, surface texture, and color may lead to uneven results when bead blasting. Small differences in the blasting process, such as nozzle distance or media flow rate, can produce uneven textures or finishes, requiring frequent adjustments and testing.
Material Compatibility
Not all plastics are suitable for bead blasting. Softer plastics like LDPE (Low-Density Polyethylene) or elastomers may deform under the impact of the abrasive media. Additionally, certain plastic formulations may react negatively to blasting, leading to discoloration, cracking, or loss of mechanical properties.
Tips for Safe and Effective Plastic Blasting
Below are key tips to ensure the process is both safe and effective:
Choose the Right Media
Not all blasting media are suitable for plastics. Fine glass beads or soft abrasives like baking soda are ideal, as they gently treat the surface without causing excessive wear or heat buildup. Avoid harsh materials like steel grit, which can damage the plastic. Selecting the right media ensures a balance between surface treatment and material integrity.
Adjust Blasting Pressure
Plastics are softer than metals and can deform or melt under excessive pressure. Use lower air pressures, typically between 20 and 40 PSI, to avoid cracking, warping, or surface damage. Start with a test piece to fine-tune the pressure before working on the component.
Maintain a Proper Distance
Keep the blasting nozzle at an appropriate distance, usually 6–12 inches from the surface. This prevents concentrated force that could overheat or distort the plastic. Moving the nozzle in a consistent, sweeping motion ensures even treatment and avoids overworking any specific area.
Monitor Heat Generation
Plastics are highly sensitive to heat, and prolonged blasting can cause softening or deformation. To manage heat buildup, use short bursts rather than continuous blasting. If necessary, incorporate cooling intervals to maintain the material’s structural integrity.
Use Protective Equipment
Safety is critical during bead blasting. Operators should wear proper personal protective equipment (PPE), including gloves, safety goggles, and respiratory masks, to protect against dust and abrasive particles. Ensure the blasting area is well-ventilated to minimize exposure to airborne contaminants.
Conclusion
Bead blasting is essential for enhancing plastic components, offering benefits like surface preparation, deburring, texturing, and cleaning. While not all plastics are suitable for this process, materials such as ABS, polycarbonate, and nylon are commonly used in industries that require high-quality finishes and functionality. Manufacturers can achieve effective and safe results by choosing the right media, adjusting blasting pressure, and maintaining proper safety measures. When performed correctly, bead blasting improves plastic parts' appearance, durability, and performance, making it a key process in plastic manufacturing.
You Might Like Also
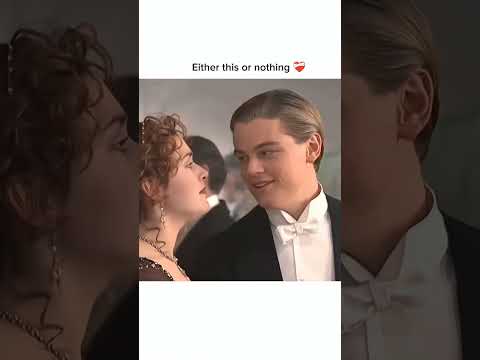
Top 10 CNC Machining Service Companies in China
If one has been wearing glasses for sHere are few Tips for Transitioning from Glasses to Contact Lenses Here are few Tips for Transitioning from Glasses to Contact Lenses Here are few Tips for Transitioning from Glasses to Contact Lenses Here are few Tips for Transitioning from Glasses to Contact Lenses ome time, they are aware of the challenges th Read More